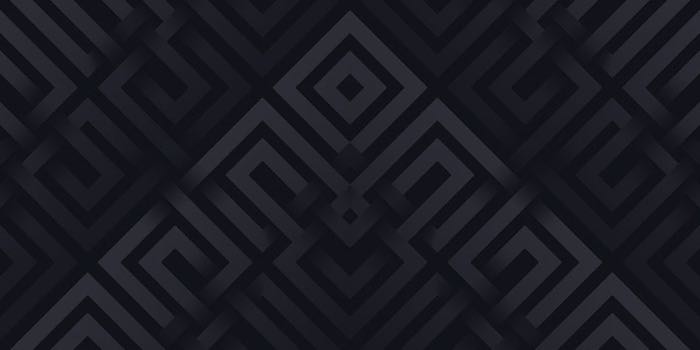
Factory production optimisation
Optimising industrial processes for hot press for Laminated Veneer Lumber products
Laminated Veneer Lumber (LVL) is a wood-derived product that consists of thinly prepared layers, called veneers, of wood/tree logs that are stacked along the fibre orientation (grain direction) and bonded together using a thermoset adhesive. This composite provides an output product, LVL, that has strong structural properties with a wide variety of strong, lightweight material applications in beams, struts, and wall elements.
LVL, as a type of wood-based composite, can be engineered to achieve specific desired structural properties. The selection and specific combination of selected wood types are known as veneer recipes whose overall strength is measured through the material property, the stiffness. Commonly, the degree of stiffness of veneer is measured by calculating its Modulus Of Elasticity (MOE) by non-destructive methods of optical or ultrasonic sensors. This measure refers to the amount of deflection the material provides, consequently, its resistance to deformation under stress. This property is highly important in the consideration of engineering designs and practical applications.
This project, in collaboration with an industry partner, will develop a machine learning model on top of the industrial process data, to enable timely and data driven process automation refinements. Several models are undergoing evaluation, including the use of recurrent neural networks and convolutional neural network approaches.
Outcomes:
• Improved material strength through ensuring LVL bonding takes place at ideal temperature and pressure.
• Higher overall material quality resulting in reduced costs through better QA/test rate.
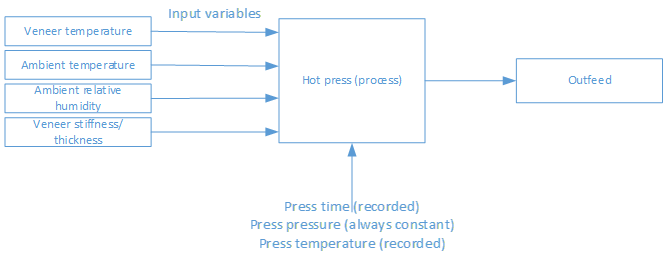
Project Team:
Dr Adil Hammadi